To an outsider, printed circuit board assembly in an age of surface mount technology may seem a little like a "paint-by-numbers" trade. However, as electronics continue to shrink in size, PCB manufacturing and assembly face new challenges and must meet a higher standard of expertise to continue servicing the most innovative electronics providers.
The smaller they are, the harder they fall
Smaller, more flexible PCBs matter as consumers expect greater capabilities from their handheld and wearable devices. Sure, working around "cumbersome" PCBs during a system assembly could lead to groundbreaking developments in electronics - according to Buzzfeed, PCB placement was the original catalyst behind the iPhone 7's jack-less design.
That example aside, other and future electronics makers will presumably manufacture PCBs that suit exact specification requirements, enlisting a PCB manufacturer and component OEMs to miniaturize their products or make them more conducive to flexible substrates - a change that will force the PCB assembly industry to rise to the occasion.
Itty-bitty PCB: Concerns over clearance and creepage
Clearance and creepage pertain to the distance between conductive materials like traces and pads on a PCB, the former defined as an "as-the-crow-flies" measurement through the air as opposed to the latter, the distance along the PCB surface between two conductive points including troughs and peaks.
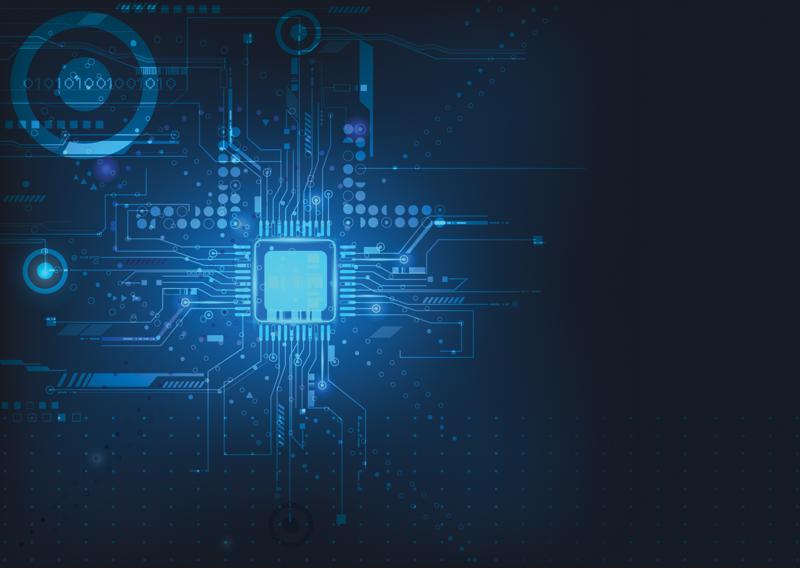
PCB and component miniaturization places added strain on PCB manufacturers to design schema capable of meeting regulations for creepage and clearance distances, thus preserving the functionality of the circuitry. PCBA, however, is charged with testing the integrity of these designs and determining the risk of overvoltage or arcing, an increasing threat as high-voltage circuits with low-voltage continue to share a single PCB in more and more industrial equipment outside the consumer electronics market. For instance, devices currently used by the military and in the health care sector are especially imperiled, as these fields are especially fond of miniaturization and flexible tech. Depending on the nature of the device, its "bendability" could shorten the clearance or creepage between conductive components and cause a short.
"Devices used by the military and in healthcare are especially imperiled."
Consummate PCBA testing may relieve micro-malfunctions
Partnering with a trustworthy PCB assembly provider with experience in mixed-voltage technology and component miniaturization could prove beneficial to electronics manufacturers hoping to develop cutting-edge handheld devices, wearables or even industrial equipment.
The reasons for such extend beyond what we've already described. Returning again to clearance and creepage in high-voltage circuitry, many factors pertaining to PCB assembly or system assembly could exacerbate adverse issues. Poor system ventilation, for example, may increase dust and debris accumulation in the air or on the PCB surface between two nodes, which in turn can incite connectivity issues. PCBA experts should have the tools and the know-how to determine whether system layout could augment device resilience against creepage and clearance or place it at risk, as well as preempt issues through consultation. The impact to finished product quality is obvious, but in terms of prototyping, catching problems early could expedite market release and save electronics manufacturers considerably on resources and labor costs.
As electronics get smaller and more versatile, risks only grow. A PCBA partner with unparalleled industry knowledge and an eye on where technology will trend can ensure the quality of your goods remains high and innovation maintains its proper course.